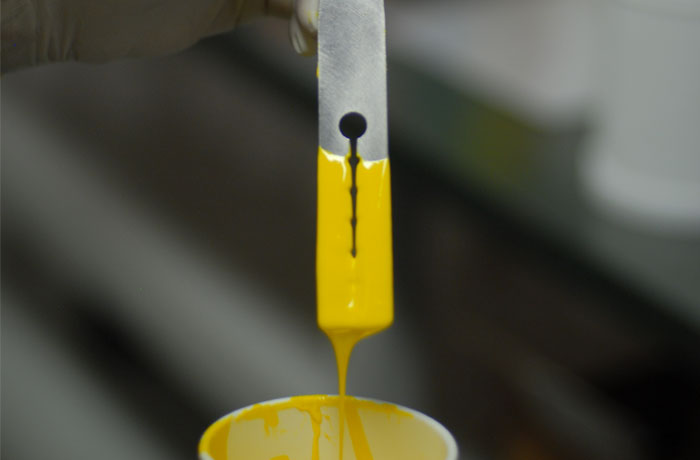
Ink Mixing - Visco Spatula Operating Instructions
Our Visco Spatula is a reusable stainless steel ink spatula that makes it easier for you to mix your inks to the correct viscosity level for your application. The Visco Spatula works by measuring the time duration for ink to flow down calibrated openings on the end of the spatula.