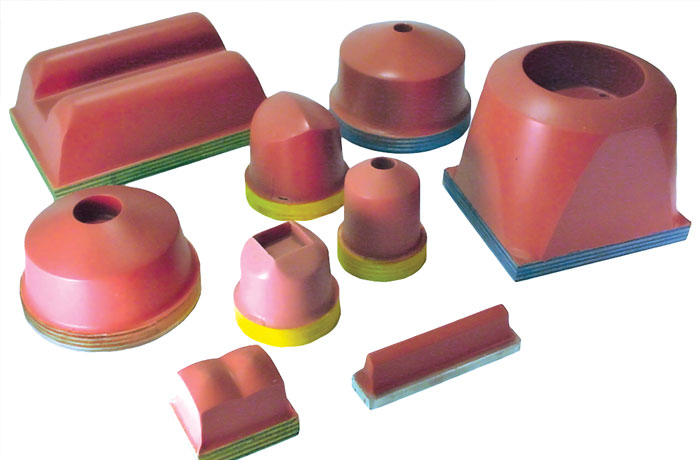
How to Select the Proper Pad for the Job
One of the most frequently asked questions in the early stages of learning the do's and don'ts of the pad printing process is, "How do I know what pad to use for this part?"
Literally there are hundreds of sizes and shapes of pads out there to choose from - and then add the next most important variable of determining which hardness of rubber to use - and the level of confusion is only compounded further. For experienced operators this question is rather simple, but for the beginner this is not an easy task.